PID controller are feedback control systems that are frequently used to maintain target temperatures in industrial operations. Three main control factors serve as their foundation: Proportional (P), Integral (I), and Derivative (D).
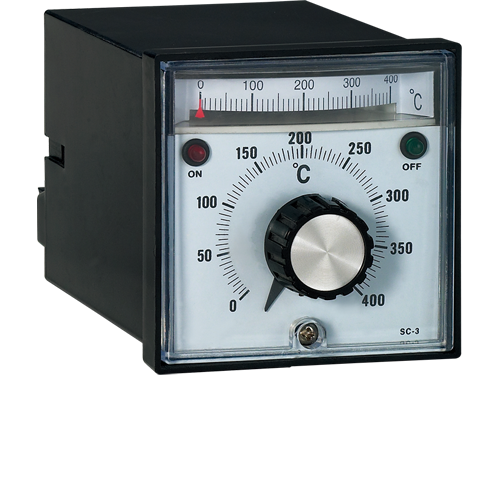
Proportionate (P)
The difference between the measured temperature and the intended setpoint temperature is known as the current error, and it is this difference that the proportional component reacts to. It modifies the output signal proportionately to the inaccuracy.
Integral (I)
The integral component considers the total of all previous mistakes over a period of time. By continually modifying the output signal in accordance with the integral of the error signal, it aids in the elimination of any steady-state error.
Derivative (D)
By taking into account the error signal’s rate of change, the derivative component forecasts upcoming mistakes. It predicts how the system will behave and modifies the output signal to offset sudden temperature swings.
Working Principle
The difference between the intended setpoint and the observed temperature is the error value that the temperature controller pid continually computes. The controller modifies the output in order to reduce error and keep the temperature at the setpoint based on this error value. The proportional, integral, and derivative terms are combined to form the output signal, each of which adds to the total control action.
PID Controller Applications
Industrial Automation: PID controllers maintain constant product quality and process efficiency by controlling the temperature in industrial ovens, furnaces, and reactors.
HVAC Systems: PID controllers are used by heating, ventilation, and air conditioning systems to maximize energy efficiency and maintain pleasant indoor temperatures.
Food processing: To ensure the safety and quality of food, PID controllers manage the temperature of appliances like ovens, fryers, and freezers.
Chemical Processes: Temperature control during chemical reactions, distillation, and polymerization is greatly aided by PID controllers.
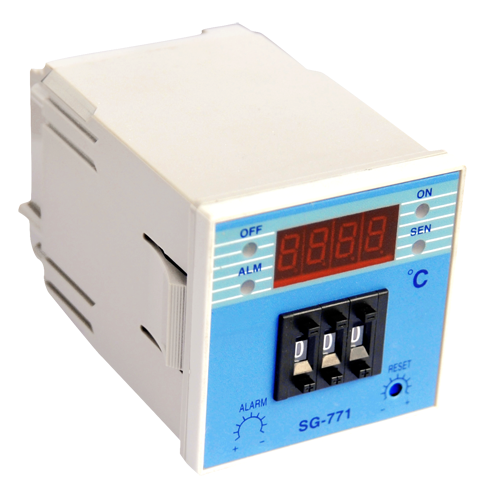
PID Controller Benefits
Temperature controller PID ensures consistency and quality in industrial operations by offering accurate temperature control.
Adaptability: Even in conditions that fluctuate, PID controllers can adjust to dynamic changes in the system and maintain stable temperatures.
Efficiency: PID controllers assist improve energy usage and save operating expenses by reducing temperature variations.
Versatility: PID controllers are extremely versatile and scalable since they may be used with a wide range of systems and processes.